五軸加工(5 Axis Machining),顧名思義,數控工具機加工的一種模式。採用X、Y、Z、A、B、C中任意5個坐標的線性插補運動,五軸加工所採用的工具機通常稱為五軸工具機或五軸加工中心。可是你真的了解五軸加工嗎?
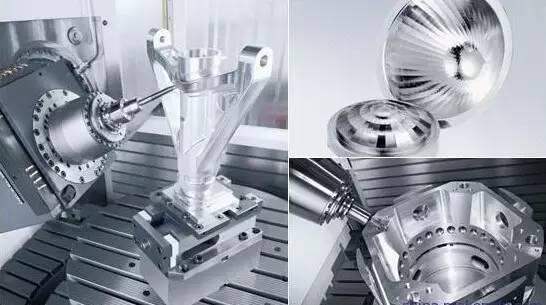
五軸技術的發展
幾十年來, 人們普遍認為五軸數控加工技術是加工連續、平滑、複雜曲面的唯一手段。一旦人們在設計、製造複雜曲面遇到無法解決的難題, 就會求諸五軸加工技術。但是…..
五軸聯動數控是數控技術中難度最大、應用範圍最廣的技術, 它集計算機控制、高性能伺服驅動和精密加工技術於一體, 應用於複雜曲面的高效、精密、自動化加工。國際上把五軸聯動數控技術作為一個國家生產設備自動化技術水平的標誌。由於其特殊的地位,特別是對於航空、航天、軍事工業的重要影響, 以及技術上的複雜性, 西方工業已開發國家一直把五軸數控系統作為戰略物資實行出口許可證制度, 對我國實行禁運, 限制我國國防、軍事工業發展。
上次金屬加工小編髮的關於「東芝工具機事件」就是基於這個封鎖制度!
與三軸聯動的數控加工相比, 從工藝和編程的角度來看, 對複雜曲面採用五軸數控加工有以下優點:
(1)提高加工質量和效率
(2)擴大工藝範圍
(3)滿足複合化發展新方向
但是,哈哈,又但是了。。。五軸數控加工由於干涉和刀具在加工空間的位姿控制,其數控編程、數控系統和工具機結構遠比三軸工具機複雜得多。所以,五軸說起來容易,真實實現真的很難!另外要操作運用好真的更難!
說到五軸,真的不得不說一說真假五軸?小編前段時間發布了一個「假五軸or真五軸?與三軸有什麼區別呢?」的文章,其實文章中主要講述了真假5軸的區別主要在於是否有RTCP功能,為此,小編專門去查找了這個詞!
RTCP,解釋一下,Fidia的RTCP是「Rotational Tool Center Point」的縮寫,字面意思是「旋轉刀具中心」,業內往往會稍加轉義為「圍繞刀具中心轉」,也有一些人直譯為「旋轉刀具中心編程」,其實這只是RTCP的結果。PA的RTCP則是「Real-time Tool Center Point rotation」前幾個單詞的縮寫。海德漢則將類似的所謂升級技術稱為TCPM,即「Tool Centre Point Management」的縮寫,刀具中心點管理。還有的廠家則稱類似技術為TCPC,即「Tool Center Point Control」的縮寫,刀具中心點控制。
從Fidia的RTCP的字面含義看,假設以手動方式定點執行RTCP功能,刀具中心點和刀具與工件表面的實際接觸點將維持不變,此時刀具中心點落在刀具與工件表面實際接觸點處的法線上,而刀柄將圍繞刀具中心點旋轉,對於球頭刀而言,刀具中心點就是數控代碼的目標軌跡點。為了達到讓刀柄在執行RTCP功能時能夠單純地圍繞目標軌跡點(即刀具中心點)旋轉的目的,就必須實時補償由於刀柄轉動所造成的刀具中心點各直線坐標的偏移,這樣才能夠在保持刀具中心點以及刀具和工件表面實際實際接觸點不變的情況,改變刀柄與刀具和工件表面實際接觸點處的法線之間的夾角,起到發揮球頭刀的最佳切削效率,並有效避讓干涉等作用。因而RTCP似乎更多的是站在刀具中心點(即數控代碼的目標軌跡點)上,處理旋轉坐標的變化。
不具備RTCP的五軸工具機和數控系統必須依靠CAM編程和後處理,事先規劃好刀路,同樣一個零件,工具機換了,或者刀具換了,就必須重新進行CAM編程和後處理,因而只能被稱作假五軸,國內很多五軸數控工具機和系統都屬於這類假五軸。當然了,人家硬撐著把自己稱作是五軸聯動也無可厚非,但此(假)五軸並非彼(真)五軸!
小編因此也諮詢了行業的專家,簡而言之,真五軸即五軸五聯動,假五軸有可能是五軸三聯動,另外兩軸只起到定位功能!
這是通俗的說法,並不是規範的說法,一般說來,五軸工具機分兩種:一種是五軸聯動,即五個軸都可以同時聯動,另外一種是五軸定位加工,實際上是五軸三聯動:即兩個旋轉軸旋轉定位,只有3個軸可以同時聯動加工,這種俗稱3+2模式的五軸工具機,也可以理解為假五軸。
怎樣?關於真假五軸的情況您了解了嗎?有新的說法,歡迎留言探討!
本次對於RTCP功能也沒有進行詳盡的描述,如果你對這方面感興趣,小編決定下次多收集一些這方面的資料,給您解答!需要的話歡迎留言!
發展五軸數控技術的難點及阻力
大家早已認識到五軸數控技術的優越性和重要性。但到目前為止, 五軸數控技術的應用仍然局限於少數資金雄厚的部門, 並且仍然存在尚未解決的難題。
下面小編收集了一些難點和阻力,看是否跟您的情況對應?
1.五軸數控編程抽象、操作困難
這是每一個傳統數控編程人員都深感頭疼的問題。三軸工具機只有直線坐標軸, 而五軸數控工具機結構形式多樣;同一段NC 代碼可以在不同的三軸數控工具機上獲得同樣的加工效果, 但某一種五軸工具機的NC代碼卻不能適用於所有類型的五軸工具機。數控編程除了直線運動之外, 還要協調旋轉運動的相關計算, 如旋轉角度行程檢驗、非線性誤差校核、刀具旋轉運動計算等, 處理的信息量很大, 數控編程極其抽象。
五軸數控加工的操作和編程技能密切相關, 如果用戶為工具機增添了特殊功能, 則編程和操作會更複雜。只有反覆實踐, 編程及操作人員才能掌握必備的知識和技能。經驗豐富的編程、操作人員的缺乏, 是五軸數控技術普及的一大阻力。
國內許多廠家從國外購買了五軸數控工具機, 由於技術培訓和服務不到位, 五軸數控工具機固有功能很難實現, 工具機利用率很低, 很多場合還不如採用三軸工具機。
2.對NC 插補控制器、伺服驅動系統要求十分嚴格
五軸工具機的運動是五個坐標軸運動的合成。旋轉坐標的加入, 不但加重了插補運算的負擔, 而且旋轉坐標的微小誤差就會大幅度降低加工精度。因此要求控制器有更高的運算精度。
五軸工具機的運動特性要求伺服驅動系統有很好的動態特性和較大的調速範圍。
3.五軸數控的NC 程序校驗尤為重要
要提高機械加工效率,迫切要求淘汰傳統的「試切法」校驗方式 。在五軸數控加工當中,NC 程序的校驗工作也變得十分重要, 因為通常採用五軸數控工具機加工的工件價格十分昂貴, 而且碰撞是五軸數控加工中的常見問題:刀具切入工件;刀具以極高的速度碰撞到工件;刀具和工具機、夾具及其他加工範圍內的設備相碰撞;工具機上的移動件和固定件或工件相碰撞。五軸數控中,碰撞很難預測,校驗程序必須對工具機運動學及控制系統進行綜合分析。
如果CAM 系統檢測到錯誤, 可以立即對刀具軌跡進行處理;但如果在加工過程中發現NC 程序錯誤,不能像在三軸數控中那樣直接對刀具軌跡進行修改。在
三軸工具機上, 工具機操作者可以直接對刀具半徑等參數進行修改。而在五軸加工中, 情況就不那麼簡單了,因為刀具尺寸和位置的變化對後續旋轉運動軌跡有直接影響。
4.刀具半徑補償
在五軸聯動NC 程序中, 刀具長度補償功能仍然有效, 而刀具半徑補償卻失效了。以圓柱銑刀進行接觸成形銑削時, 需要對不同直徑的刀具編制不同的程序。目前流行的CNC 系統均無法完成刀具半徑補償,因為ISO文件中沒有提供足夠的數據對刀具位置進行重新計算。用戶在進行數控加工時需要頻繁換刀或調整刀具的確切尺寸, 按照正常的處理程序, 刀具軌跡應送回CAM 系統重新進行計算。從而導致整個加工過程效率十分低下。
針對這個問題, 挪威研究人員正在開發一種臨時解決方案, 叫做LCOPS(Low Cost Optimized ProductionStrategy , 低耗最優生產策略)。刀具軌跡修正所需數據由CNC 應用程式輸送到CAM 系統, 並將計算所得刀具軌跡直接送往控制器。LCOPS 需要第三方提供CAM 軟體, 能夠直接連接到CNC 工具機, 其間傳送的是CAM 系統文件而不是ISO 代碼。對這個問題的最終解決方案, 有賴於引入新一代CNC 控制系統, 該系統能夠識別通用格式的工件模型文件(如STEP 等)或CAD 系統文件。
5.後置處理器
五軸工具機和三軸工具機不同之處在於它還有兩個旋轉坐標, 刀具位置從工件坐標系向工具機坐標系轉換, 中間要經過幾次坐標變換。利用市場上流行的後置處理器生成器, 只需輸入工具機的基本參數, 就能夠產生三軸數控工具機的後置處理器。而針對五軸數控工具機, 目前只有一些經過改良的後置處理器。五軸數控工具機的後置處理器還有待進一步開發。
三軸聯動時, 刀具的軌跡中不必考慮工件原點在工具機工作檯的位置, 後置處理器能夠自動處理工件坐標系和工具機坐標系的關係。對於五軸聯動, 例如在XYZBC 五軸聯動的臥式銑床上加工時, 工件在C 轉台上位置尺寸以及B 、C 轉台相互之間的位置尺寸, 產生刀具軌跡時都必須加以考慮。工人通常在裝夾工件時要耗費大量時間來處理這些位置關係。如果後置處理器能處理這些數據, 工件的安裝和刀具軌跡的處理都會大大簡化:只需將工件裝夾在工作檯上, 測量工件坐標系的位置和方向, 將這些數據輸入到後置處理器, 對刀具軌跡進行後置處理即可得到適當的NC 程序。
6.非線性誤差和奇異性問題
由於旋轉坐標的引入, 五軸數控工具機的運動學比三軸工具機要複雜得多。和旋轉有關的第一個問題是非線性誤差。非線性誤差應歸屬於編程誤差, 可以通過縮小步距加以控制。在前置計算階段, 編程者無法得知非線性誤差的大小, 只有通過後置處理器生成工具機程序後, 非線性誤差才有可能計算出來。刀具軌跡線性化可以解決這個問題。有些控制系統能夠在加工的同時對刀具軌跡進行線性化處理, 但通常是在後置處理器中進行線性化處理。
旋轉軸引起的另一個問題是奇異性。如果奇異點處在旋轉軸的極限位置處, 則在奇異點附近若有很小振蕩都會導致旋轉軸的180°翻轉, 這種情況相當危險。
7.對CAD/ CAM系統的要求
對五面體加工的操作, 用戶必須藉助於成熟的CAD/CAM 系統, 並且必須要有經驗豐富的編程人員來對CAD/CAM 系統進行操作。
8.購置工具機的大量投資
以前五軸工具機和三軸工具機之間的價格懸殊很大。現在, 三軸工具機附加一個旋轉軸基本上就是普通三軸工具機的價格, 這種工具機可以實現多軸工具機的功能。同時, 五軸工具機的價格也僅僅比三軸工具機的價格高出30 %~ 50 %。
除了工具機本身的投資之外, 還必須對CAD/CAM系統軟體和後置處理器進行升級, 使之適應五軸加工的要求;必須對校驗程序進行升級, 使之能夠對整個工具機進行仿真處理。
國內外典型的五軸加工中心
下面小編為您介紹幾款國內外典型的五軸加工中心:
1. 哈默C52加工中心
德國哈默(Hermle)公司的C52加工中心是搖籃式雙擺工作檯五軸加工工具機,適用於航空航天、模具製造、能源和半導體工業,其外觀和主要技術規格如圖所示。

哈默C52加工中心
從圖中可見,搖籃式雙擺工作檯採用縱向布局,迴轉工作檯直徑為f 1 000mm,由力矩電動機直接驅動,結構緊湊,最高轉速為500r/min。搖籃採用伺服電動機和無背隙齒輪傳動,擺動範圍為+100°/-130°,可以進行五軸聯動的立/臥式車削加工或五軸聯動銑削加工和5面銑削加工。車削時工作檯最大載荷為1 000kg,銑削時工作檯最大載荷為2 000kg,可以從工具機上方裝卸較重的大型工件。
為了提高工具機的動態性能,哈默公司研發了獨特的總體結構配置:移動部件輕量化。框架式主軸十字滑座在高台式床身的頂部,完成X-Y方向移動,主軸滑枕作Z軸垂直方向移動,採用盤式刀庫,如圖所示。
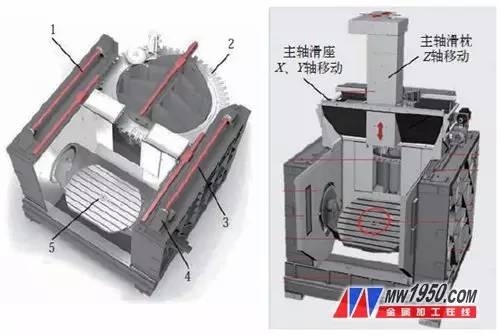
哈默C52加工中心的總體結構配置
1.線性導軌 2.刀庫 3.滾珠絲槓 4.伺服驅動 5.雙擺工作檯
從圖中可見,主軸下層滑座由安裝在床身左右兩側壁上的伺服電動機和滾珠絲槓沿3根線性導軌移動,以實現重心驅動,避免移動過程的偏斜,提高了工具機的工作精度。
哈默C52加工中心在車銑複合加工時採用海德漢640數控系統,包括提高動態效率的主動顫振控制、自適應進給控制和提高動態加工精度的主動振動阻尼、載荷自適應控制等智能模塊。
2. 西田YMC430-II精密加工中心
日本西田(Yasda)公司的YMC430-II精密加工中心主要用於加工微小的高精度零件,在結構設計上特別注意提高剛度和減少熱變形的影響,其總體結構配置如圖所示。
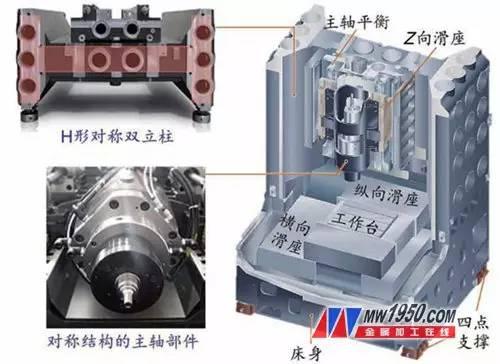
西田YMC430-II精密加工中心的總體結構配置
從圖中可見,橫截面呈H形的、左右前後4個方向都對稱和斷面係數大的整體龍門式雙立柱,保證了工具機結構的高剛度、高精度和熱穩定性。主軸滑座和主軸部件位於H形立柱的正前方,具有重量平衡系統,以保證Z軸移動的精度,結構對稱,基本上抵消熱變形所引起的刀具中心點相對工作檯的偏移量。
YMC430-I I加工中心的X、Y、Z軸皆由相互對稱配置2個直線電動機驅動,行程範圍分別為420mm、300mm和250mm,快速進給20m/min,採用高剛度和高精度的線性導軌(小直徑滾珠、8滾道循環、加長型滑塊)導向,以提高移動精度和剛性,簡化機械結構,避免反向背隙,保證工具機的動態性能。
主軸轉速範圍2 0 0 ~ 4 0 0r/min,在主軸滑座下方配置有盤式刀庫,標配容量32把刀,刀具最大直徑f 50mm,刀具最大長度120mm,刀具最大重量500g。
該 機 床 的 平 移 工 作 台 面 積為600mm×350mm,其上安裝R10型雙擺工作檯,B軸擺動範圍-10°/+100°,C軸360°迴轉,從而構成五軸聯動加工工具機,最大加工直徑250mm。主軸的定位精度在全行程範圍內的實際測量值分別為0.508μm、0.356μm和0.316μm,X-Y運動軸的圓度為0.60μm。B、C迴轉軸的雙向定位精度分別為0.95sec和1.19sec。在加工圓錐表面時圓度為1.24μm,皆明顯高於同類工具機。
完善的熱管理系統是YMC430-I I工具機的最大特點之一,是保證工具機高精度的關鍵。工具機的冷卻部位循環原理如圖所示。

西田YMC430-II的冷卻部位和循環系統
從圖中可見,工具機在6個部位配置循環液冷卻系統:①立柱的內冷卻。②主軸頭的內冷卻。③主軸滑座的內冷卻。④X軸直線電動機的冷卻。⑤Y軸直線電動機的冷卻。⑥Z軸直線電動機的冷卻。製冷裝置輸出溫度較低的冷卻液進入各冷卻部位,將熱量帶出,溫度較高的冷卻液再回到熱交換器中再度進行製冷。
3. 米克朗 HSM 600U LP高速加工中心
GF加工方案集團旗下的米克朗公司生產多種型號的高速(HSM)、高性能(HPM)和高效率(HEM)加工中心。其中HSM 600U LP加工中心是在原有HSM系列的基礎上改進設計而成,工作檯直徑600mm,最大載荷120kg,適合模具製造和其他中小批量精密製造企業加工高精度和高表面質量的零件,工具機的外觀和結構如圖所示。
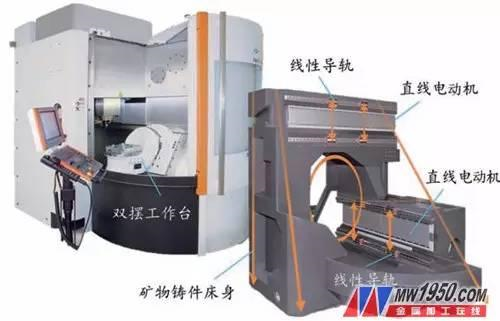
HSM 600 ULP加工中心的外觀和結構
從圖中可見,該工具機的3個移動軸X、Y、Z和2個迴轉軸B、C皆採用直接驅動方式。工具機的床身、立柱和橫樑為一個整體封閉結構,上窄下寬,呈金字塔形,採用礦物鑄件(樹脂混凝土),具有良好的阻尼特性,保證了工具機的剛度和穩定性。中間有O形孔道,以便與托板交換裝置或刀庫聯結。線性導軌布置在直線電動機的兩側,使兩線性導軌之間的有較大的距離,驅動力儘可能在移動部件的重心。
工具機採用STEP TEC智能電主軸,最高轉速30 000/36 000/42 000r/min可選。其intelliSTEP智能化系統可以控制和優化電主軸的工況。例如,主軸端軸向位移、溫度、振動和刀具拉杆位置等,預測主軸在不同工況下的工作壽命。
該工具機的另一重要特點是「聰明工具機」軟體。包括工具機保護、提高加工精度和提高生產力3個方面。例如,智能溫度控制、操作支持系統、高級加工過程和遠距簡訊通知等。
五軸加工工具機未來智能化趨勢
智能裝備的控制模式和人機介面將會有很大的變化,WiFi寬頻、藍牙近距通信等網絡性能的提高,基於平板電腦、手機和穿戴設備等基於網絡的移動控制方式會越來越普及。與時俱進的觸摸屏和多點觸控的圖形化人機介面將逐步取代按鈕、開關、滑鼠和鍵盤。人們,特別是年輕人已經習慣智能電子消費產品的操作方式,能夠快速做出反應,切換螢幕,上傳或下載數據,從而大大豐富了人機互動的內容,同時明顯降低誤操作率。例如,對數控工具機的操作可以通過筆記本、平板電腦和智慧型手機在WiFi環境下進行,如圖所示。

在WiFi環境下的人-機和機-機通信
從圖中可見,不僅人機的交互方式從控制面板延伸到移動終端,設備和工具之間也可以進行物與物的通信。工具機的加工精度和效率在很大程度上取決於刀具的狀態,如果在刀具或刀柄上嵌入晶片,就成為智能刀具。晶片不僅可以記錄在刀具預調儀上進行調整時的數據,還可以記錄刀具在工具機的進行了多長的切削時間,還有多少剩餘壽命,可以加工幾個零件等都可以讓操作者和有關部門了如指掌,減少停機和更換刀具的時間。智能刀具及其管理的概念如上圖所示。
在不同的加工情況下,往往需要設備具有不同的性能,可以根據設備工況的統計分析,可從設備供應商或第三方APP應用軟體商店購買和下載不同的軟體,以提高設備精度、加工速度或節能等,如圖所示。

提高設備性能的APP應用軟體商店
智能工廠的數控工具機和機器人等智能裝備的未來發展重點已經不在硬體,感知外部環境和工況變化需要更加強大的計算能力、通信帶寬和速度,才能進行實時控制,形成真正的信息物理融合系統。它的特點是將設備的控制分為計算和過程兩部分,把運動控制保留在本地,而將計算移到雲端,在雲端「克隆」相應的虛擬設備,在雲端進行虛擬製造,如圖所示。

過程和計算分離的雲數控系統
從圖中可見,需要計算能力的數控核心、可編程控制、圖形人機介面和通信等模塊構成設備群的雲端控制系統,通過中間件控制虛擬工具機1、虛擬工具機2、虛擬工具機n,同時通過乙太網接口下傳至車間的路由器,連接不同工具機的控制器,控制相應工具機的運動,從而將虛擬工具機與實體工具機構成一對一的仿真和監控系統。
本文參考文獻如下:《五軸加工工具機:現狀和趨勢》作者:專家張曙、《工具機工業亟需發展五軸數控技術》作者:清華大學 游華雲 葉佩青等、《高效五軸加工技術與工具機》作者: 周孫良、《五軸加工的RTCP技術》等。